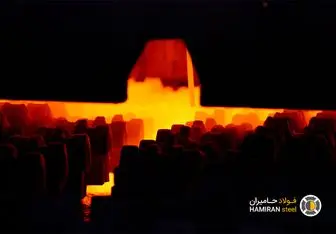
عملیات حرارتی فلزات به هزاران سال قبل برمی گردد. کشف فرآیند های عملیات حرارتی بدون شک به ایجاد دوره قابل توجهی از پیشرفت تکنولوژی کمک کرد. علاوه بر این، چندین فرآیند ماشینکاری و متالورژی به لطف این روش، اکنون از فناوری های پیشرفته برای تولید قطعات با خواص دلخواه و باکیفیت تر استفاده میکنند.
امروزه روش های مختلف عملیات حرارتی در بسیاری از صنایع استفاده می شود. این فرآیند های عملیات حرارتی به تغییر خواص فیزیکی و گاهی شیمیایی فلز برای اهداف مختلف کمک می کند. در اینجا، همه آنچه را که باید در مورد فرآیندهای عملیات حرارتی، مزایای آنها و انواع عملیات حرارتی برای فولاد بدانید، بررسی خواهیم کرد.
عملیات حرارتی چیست؟
تا حد زیادی عملیات حرارتی یکی از حیاتی ترین اجزای فرآیند پردازش فولاد است. این شامل گروهی از تکنیک های حرارتی و فلزکاری است که خواص فلز را تغییر می دهد.
به طور دقیق، عملیات حرارتی خواص فیزیکی، مکانیکی و گاهی شیمیایی فلزات را از طریق گرمایش و سرمایش و یا تغییر ترکیب شیمیایی سطح تغییر می دهد. این ویژگی ها عبارتند از شکل پذیری، سختی، مقاومت در برابر دما، ماشین کاری، استحکام و غیره.
روش های عملیات حرارتی بسته به نوع مواد فلزی و خواص مورد نیاز متفاوت است. برای سازندگان مهم است که روش عملیات حرارتی مناسب را برای رفع نیاز های خاص خود را بدانند.
کدام فلزات برای عملیات حرارتی پذیر مناسب هستند؟
قابل ذکر است، شما باید هر ماده را بررسی کنید تا روش عملیات حرارتی صحیح را برای بدست آوردن خواص مورد نیاز انتخاب کنید. این به این دلیل است که همه مواد فلزی برای همه انواع عملیات حرارتی مناسب نیستند. فلزات آهنی بیشتر مواد عملیات حرارتی شده را تشکیل می دهند. بنابراین، گرید های مختلف فولاد حدود 80 درصد از فلزات عملیات حرارتی شده را تشکیل می دهند. با این حال، برخی از مواد غیر آهنی نیز برای عملیات حرارتی مناسب هستند.
به این ترتیب، آلیاژ های فلزی مانند مس، آلومینیوم، نیکل، برنج، منیزیم و تیتانیوم تحت عملیات حرارتی قرار می گیرند.
در زیر برخی از فلزات موجود برای عملیات حرارتی و انواع عملیات حرارتی مناسب آورده شده است.
1. چدن، فولاد کربن، فولاد ضد زنگ مارتنزیتی، و فولاد ابزار
روشهای عملیات حرارتی
سطحی : حرارتی-شیمیایی، کربورایزینگ، نیتروژن دهی، کربونیتروژن دهی
حجمی: تمپر، سخت کاری، نرماله، آنیل
2. مس و آلیاژهای مس
روش های عملیات حرارتی - آنیل کردن، پیری و کوئنچ.
3. آلومینیوم
روش های عملیات حرارتی - آنیل، عملیات حرارتی محلول، پیری سختی.
مراحل عملیات حرارتی فلز
به طور کلی، چهار روش اصلی عملیات حرارتی برای فلزات وجود دارد. این فرآیندها عبارتند از: سختکاری، نرمالیزاسیون، بازپخت و تمپرینگ.
صرف نظر از این، توجه داشته باشید که سه مرحله اولیه در عملیات حرارتی فلزات وجود دارد. این مراحل عبارتند از گرم کردن، نگه داشتن در دمای مورد نظر و سرد کردن. به مراحل زیر نگاهی بیندازید:
1. مرحله گرمایش
این اولین مرحله در هر فرآیند عملیات حرارتی برای فلزات است. بسیاری از آلیاژ ها زمانی که تا دمای 1200 درجه سانتیگراد گرم می شوند، بسته به گرید فلز، دچار تغییرات ساختاری می شوند. علاوه بر این، ساختار آلیاژها در دمای اتاق به صورت یک محلول جامد میباشد.
این مرحله باید با دقت کافی انجام شود. و این به این دلیل است که یک حرکت اشتباه در حین گرم کردن می تواند منجر به ترک خوردن یا بد شکل شدن فلز شود. از این رو، هدف اصلی اطمینان از گرم شدن یکنواخت فلز در مرحله گرمایش است. علاوه بر این، عوامل متعددی در هنگام تعیین نرخ گرمایش قابل اعمال نقش دارند.
2. زمان نگه داشتن نمونه در دمای مورد نظر
این مرحله قسمت فلزی گرم شده شما را در دمایی نگه می دارد که تغییرات مورد نظر در ساختار فلزی رخ می دهد. علاوه بر این، فلز باید در آن دما بماند تا زمانی که کل قطعه به طور یکنواخت گرم شود.
این قسمت به مدت زمانی که فلز را در دمای مناسب نگه می دارید، اشاره دارد. شما می توانید زمان نگهداری را از طریق تجزیه و تحلیل شیمیایی، جرم و ضخامت فلز تعیین کنید - به طور کلی، هر چه جرم فلز بیشتر باشد، زمان طولانی تر می شود. با این حال، زمان نگهداری کردن بسته به مواد فلزی متفاوت است، اما معمولاً 2 ساعت طول می کشد.
3. مرحله خنک کردن
بعد از گرم کردن فلز و نگهداشتن آن در دمای مورد نظر، مرحله بعدی خنک کردن آن است. هدف اصلی مرحله خنک سازی کاهش دمای فلز به دمای اتاق است. اما پس از آن، مرحله خنک سازی خواص حاصل از فلز عملیات حرارتی شده شما را تعیین میکند.
در اینجا دوباره ، فلز ممکن است از ترکیبی به ترکیب دیگر تغییر کند، ثابت بماند یا به شکل اولیه خود بازگردد. توجه داشته باشید که این بستگی به نوع فلز، سرعت خنک کننده و محیط خنک کننده شما دارد. در نتیجه، مرحله خنک سازی برای انطباق ساختارها و خواص خاص با فلز شما حیاتی است.
عوامل موثر بر فرآیند عملیات حرارتی فلزات
عوامل مختلفی بر فرآیند عملیات حرارتی فلزات تأثیر می گذارد. این عوامل را در زیر بررسی کنید:
1. اثر زمان و دما
شاید زمان و دما مهمترین عوامل موثر بر عملیات حرارتی فلزات باشند. آنها در مراحل گرمایش، نگهداشتن و سرد کردن در عملیات حرارتی فلزات وارد بازی می شوند.
علاوه بر این، مطالعات نشان داده اند که زمان و دما نقش اساسی در تغییرات خواص مکانیکی و ریز ساختار در طی عملیات حرارتی دارند. به عنوان مثال، افزایش سرعت سرد شدن فولاد (کوئنچ) به میزان 1000 درجه سانتیگراد در دقیقه یک ریزساختار جدید به نام مارتنزیت ایجاد می کند.
2. مقدار تغییر شکل
در اغلب موارد، فرآیند های عملیات حرارتی مختلف منجر به تغییر شکل قطعات و تغییرات ابعاد آنها می شود. گذشته از این، میزان تغییر شکل به موارد زیر مرتبط است:
ساختار مواد فلزی قبل از عملیات حرارتی.
روش عملیات حرارتی.
توزیع تنش.
بنابراین، فرآیند عملیات حرارتی ممکن است بر تغییر شکل فلزات تأثیر می گذارد.
3. اثر ترکیب
عناصر آلیاژی نیز بر عملیات حرارتی فلزات تأثیر می گذارند. این به این دلیل است که آنها تمایل دارند انتشار اتم ها را از طریق شبکه های آهن به تاخیر بیندازند، بنابراین تبدیل های آلوتروپیک را به تاخیر می اندازند.
علاوه بر این، عناصر آلیاژی مانند منگنز، مولیبدن، نیکل و بور باعث افزایش سختی می شوند. به طور مشابه، این عناصر همچنین اجازه می دهند تا در دما های بالاتر برای ایجاد شکل پذیری بهتر، تلطیف شوند. از این رو، ترکیب فلز بر فرآیند عملیات حرارتی تأثیر می گذارد.
انواع عملیات حرارتی برای فولاد
چهار نوع اساسی از فولاد عملیات حرارتی در فرآوری صنعتی وجود دارد که در ادامه به بررسی آنها می پردازیم.
1. سختکاری
این نوع عملیات حرارتی با افزایش مقاومت ساختار شبکه، سختی و استحکام فولاد را بهبود می بخشد. سخت شدن شامل حرارت دادن فلز تا دمای مورد نیاز بین 800 تا 900 درجه سانتیگراد و سپس سرد شدن سریع آن است. گرید فولاد معمولاً با فرو بردن فلز داغ در یک محیط خاموش کننده مانند روغن، آب یا آب نمک خنک می شود.
اما برای گرید فولادی با محتوای بالای عناصر آلیاژی، دمای حرارت مورد نیاز از 980 تا 1110 درجه سانتی گراد متغیر است. بیشتر مواد فولادی نیاز به خنک سازی سریع دارند، زیرا مرحله خنک سازی بر سطح سختی تأثیر میگذارد.
اما پس از آن، متوجه خواهید شد که هیچ مزیتی برای سخت شدن وجود ندارد. این به این دلیل است که در حالی که سخت شدن در عملیات حرارتی فولاد افزایش می یابد، شکل پذیری به طور همزمان کاهش می یابد. بنابراین، این ماده فولاد را شکننده تر می کند.
2. تمپر کردن
اغلب متوجه میشوید که فولاد برای فرآیند های تولید پس از سخت شدن، سفتتر از حد لازم و شکنندهتر است. این به دلیل تنش داخلی شدیدی است که در طی سرد شدن سریع در عملیات حرارتی فولاد ایجاد می شود. بنابراین، تمپر یا برگشت باعث کاهش استرس داخلی و کاهش شکنندگی فولاد پس از سخت شدن می شود.
این عملیات حرارتی شامل حرارت دادن فولاد تا دمای مورد نیاز بین 125 تا 700 درجه سانتیگراد . سپس با دما و زمان مناسبی خنک میشود این عملیات باعث کاهش اندک سختی فولاد سخت شده میشود و از شکنندگی فولاد میکاهد.
علاوه بر این، تمپر فولاد شامل سه مرحله اصلی است که عبارتند از:
حرارت دادن مواد فولادی تا دمای مورد نیاز از 260 تا 760 درجه سانتیگراد بسته به گرید فولاد.
نگه داشتن گرید فولاد برای حفظ دما برای مدت زمان مورد نیاز و سپس آن را به آرامی به دمای اتاق برگردانید. با این حال، سرعت خنک شدن از دمای بازپخت بسته به فلز متفاوت است. از این رو، بر خلاف سخت شدن، بازپخت شامل خنک کردن فولاد به آرامی برای ایجاد نرمی است.
3. آنیل
معمولا فرایند آنیل را به هر نوع عملیاتی که باعث تشکیل ساختاری به جز مارتنزیت و با سختی کم و انعطاف پذیری زیاد شود گفته میشود.
فرایند آنیل بر اساس دمای عملیات، روش سرد کردن، ساختار و خواص نهایی تقسیم بندی میشود که عبارت است از:
- آنیل کامل
- آنیل همدما
آنیلینگ به دلیل استحکام و نرمی کم برای فولاد کم کربن مناسب ترین است. این روش عملیات حرارتی خواص فلز را در مقابل سخت شدن فراهم می کند. بنابراین، بازپخت فلز به کاهش تنش داخلی، افزایش انعطاف پذیری، نرم شدن فلز و اصلاح ساختار های دانه آن کمک می کند.
قطعه فلزی به آرامی با دفن قسمت فولادی داغ در خاکستر، ماسه یا سایر موادی که به آسانی گرما را در فرآیندی به نام بسته بندی منتقل نمی کنند، خنک می شود. به همین ترتیب، خنک سازی از دمای بازپخت با خاموش کردن کوره و اجازه دادن به کوره و قسمت فولادی برای خنک شدن با هم در فرآیندی به نام خنک سازی کوره انجام میشود.
4. نرماله کردن
نرماله کردن، تنش داخلی را از فلزات آهنی تولید شده با روش های مختلف حذف می کند. آنها شامل عملیات حرارتی، ماشینکاری، جوشکاری، آهنگری، ریخته گری یا شکل دهی هستند. با این حال، فولاد های نرمال شده سخت تر و قوی تر از فولاد آنیل شده هستند. در نتیجه، نرمال سازی معمولاً برای قطعات فولادی در معرض ضربه انجام می شود. علاوه بر این، این روش عملیات حرارتی برای قطعاتی که به حداکثر چقرمگی و مقاومت در برابر تنش خارجی نیاز دارند نیز استفاده می شود.
نرمال سازی فولاد شامل موارد زیر است:
حرارت دادن مواد فولادی تا دمای خاص بین 810 تا 930 درجه سانتیگراد بسته به درجه فولاد.
نگه داشتن فلز برای گرم شدن یکنواخت.
سپس آن را در هوای ساکن خنک کنید، پس بر خلاف فرایند آنیل قطعه را در هوا خنک میکنیم.
مزایای عملیات حرارتی برای فلزات
عملیات حرارتی مواد فلزی به تغییر خواص آنها کمک می کند و آنها را در فرآیند های مختلف تولید فلز قابل استفاده می کند. در زیر برخی از مزایای فلزات حرارتی آورده شده است:
سختی را چه روی سطح یا ازحجم قطعه افزایش می دهد.
عملیات حرارتی آنیل و نرماله باعث انعطاف پذیری و ماشین کاری فلزات می شود.
سختکاری به بهبود مقاومت در برابر سایش و شکنندگی فلزات کمک می کند.
فلزات عملیات حرارتی می توانند خواص الکتریکی و مغناطیسی فلز را بهبود بخشند. این باعث افزایش سازگاری آنها با سایر مواد می شود.
نتیجه
فرآیند های عملیات حرارتی در چندین فرآیند تولید به یک عنصر اصلی تبدیل شده اند. قبل از عملیات حرارتی فلزات، سازندگان باید روی یک فلز مناسب مستقر شوند. علاوه بر این، این شامل ارزیابی خواص مختلف با نیاز های پروژه است. پس از در نظر گرفتن همه عوامل، خدمات عملیات حرارتی فلز با کیفیت ضروری می شود.
برای اطلاع از قیمت انواع فولاد های قابل عملیات حرارتی از جمله قیمت فولاد mo40 و قیمت فولاد ck45 ، کافیست با شرکت فولاد حامیران ارتباط برقرار کنید تا تیم فروش و مشاوران حرفه ای ما، شما را راهنمایی کنند.