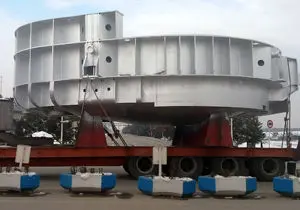
مدیر تولید فولاد ناحیه فولادسازی گفت: راکر کوره های فعلی به دلیل افزایش ظرفیت کوره ها، عمر زیاد و فرسودگی، عمدتاً دچار دفرمگی و شکست از نواحی مختلف شده که همین موضوع باعث توقفات طولانی مدت کوره ها برای تعمیر و جوشکاری آنها می شود.
محمد علی توحیدی اظهار داشت: هزینه تمام شده راکر بومی یک سوم هزینه سه سال گذشته شرکت های سازنده خارجی است.
کارشناس کوره های قوس الکتریکی فولاد مبارکه هم، گفت: در یک برنامه ریزی و هماهنگی با دفتر فنی تعمیرات از دو سال قبل بازطراحی و ساخت دو دستگاه از این تجهیز استراتژیک (مربوط به کوره های زوج و فرد که متقارن هستند)، در دستور کار ناحیه فولادسازی قرار گرفت و در مرحله اول به دلیل اینکه نقشه ابعادی و ساخت برای این تجهیز وجود نداشت، در تعمیرات برنامه ریزی شده توسعه ۷.۲ میلیون تن شرکت و تعمیرات کوره یک فولادسازی، نسبت به نقشه برداری و تهیه نقشه ساخت از طریق واحد مهندسی معکوس اقدام شد.
مهدی رستاقی افزود: پس از صحهگذاری مجدد نقشههای تهیه شده توسط مهندسی معکوس و طی فرآیند انتخاب شرکت سازنده داخلی و ابلاغ به آن، ساخت تجهیز مذکور از دی ماه سال ۱۳۹۴ آغاز شد.
وی بیان داشت: در فرآیند ساخت از زمان تأمین متریال تا پایان کار، بازرسیهای متعدد از قبیل بازرسیهای جوش، تست جوش، بازرسی های ابعادی قطعه، بازرسی جنس متر یال و رنگ، رفع ابهامات و ایرادهای نقشه ها توسط گروهی متشکل از تعمیرات ناحیه، واحد بومی سازی و خدمات فنی و پشتیبانی ناحیه نیز انجام شد.
کارشناس کوره های قوس الکتریکی شرکت فولاد مبارکه افزود: این تجهیز ۹۰ تنی با ۱۰ متر و ۸۰ سانتیمتر طول، ۸ متر و ۹۰ سانتیمتر عرض و ۶ مترو ۱۵ سانتیمتر ارتفاع به دلیل ابعاد و تناژ بالا با تمهیدات خاصی به شرکت حمل شد.
رستاقی درباره مزایای ساخت داخل این تجهیز خاطرنشان کرد: هزینه تمام شده ساخت داخل این تجهیز به میزان حدود یک سوم هزینه قیمت استعلامی سه سال قبل شرکت های سازنده خارجی است.
وی افزود: با توجه به اینکه در حال حاضر امکان استفاده از این تجهیز در کوره های ۳، ۴، ۵ و ۶ وجود دارد، بنابراین به گونهای برنامه ریزی شده است تا در جریان انجام تعمیرات برنامه ریزی شده بلندمدت کوره های قوس الکتریکی نسبت به تعویض و نصب آن اقدام شود.